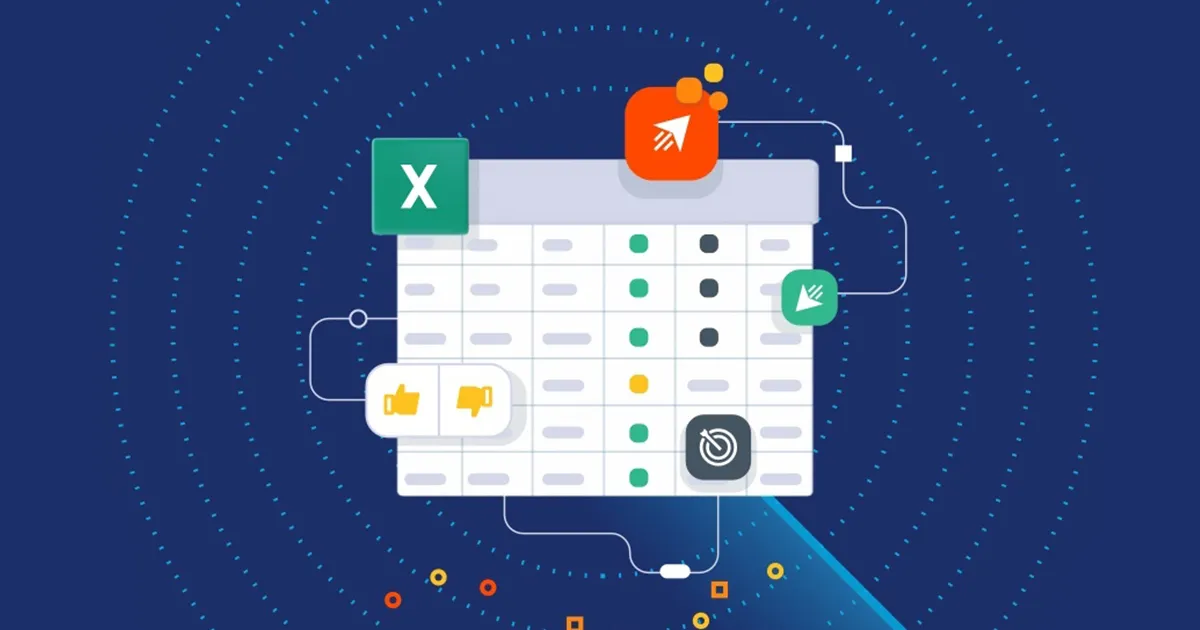
A bill-of-materials (BOM) is a crucial piece of information within manufacturing. It streamlines the manufacturing process through a detailed structure and plan that improves the efficiency of procurement teams and reduces waste. During manufacturing, product development operations run effectively the more accurate and easily manageable a BOM is. This is why a proper BOM management tool is essential.
A BOM tool generally helps teams manage their bill of materials or parts list. It identifies stock amounts necessary for a product, informs teams of possible vulnerabilities, updates upper management production line processes, and provides information on raw materials for procurement teams. There are different types of BOM software on the market today, but only a few can meet the specificity required within the electronic component industry.
Spreadsheets, like Excel, can only handle so much data and are too simple for complex multi-level or indented BOMs. It can be easy to overlook parts when a spreadsheet is several hundred or thousand long, especially since each component needs to be tracked appropriately. Engineering and manufacturing BOMs are extremely detailed with part names, manufacturer part numbers (MPNs), part descriptions, quantities, and more data that comprise a single BOM.
Tools like Microsoft Excel and Google Sheets present themselves as cost-effective solutions. Still, the probability of errors, improper orders, and wasted time far outweighs their simple user interfaces and low price. The bottom line is that spreadsheets do not include the proper functionality to track components, compare part offers, present and include alternates, and alert users to vulnerabilities.
Furthermore, it makes it far more challenging to share and distribute this information to other teams that might need help understanding the flat layout, which is often overcrowded. This impacts collaboration among company teams, decreasing the rate of production. This can be avoided with a BOM tool that enables state of the art, digital BOM management practices.
What Attributes Should a BOM Tool Have?
At its core, a digital BOM tool helps manage BOMs and the included parts. A BOM management tool should present engineers with an understandable blueprint and aid procurement teams by increasing time efficiency in purchasing. Spreadsheet tools often result in outdated or inaccurate information entering a BOM due to manual data entry. Human error is a leading cause of inaccuracies on BOMs. This erroneous data can cause issues in the production process later on, such as delays or recalls from incorrect parts or improper quantities ordered.
Similarly, spreadsheets can make change management problematic, especially with multilevel BOMs. It is hard to find the relevant product lines to update on a spreadsheet if it consists of thousands of components with no easy way to link products. Visibility into the production process suffers and increases time and materials waste if data is not updated when market changes occur.
With these problems in mind, here is what you should look for in a BOM management tool that prevents these issues, increases productivity, and provides ease of use.
1. Supply Comprehensive Data on Components: A good BOM management tool should aid users in quickly presenting accurate part information for each component. This includes technical data sheets on offered parts that procurement teams can share with engineers or other team members to confirm a part if necessary. Due to the probability of inaccurate information with manual input, a BOM management tool should also allow users to run their parts list against an extensive PCB CAD library that can help illuminate erroneous information and aid users in replacing it with accurate data.
2. Display Alternates or Drop-in Replacements: Electronic components aren’t meant to last forever, neither are their product lines. Through the course of its lifecycle, an electronic component can be not recommended for new design (NRND), end-of-life (EOL), last-time-buy (LTB), obsolete, discontinued, counterfeit, sole source, or otherwise unavailable. Continued technology integrations in different industries are set to increase the demand for components yearly, which means unavailability will become more common. An innovative BOM tool should provide smart provide form-fit-function (FFF) alternate, equivalent, or drop-in replacement (DIR) components.
The importance of knowing part alternates and their subsequent offers helps procurement and engineering teams better strategize for future disruptions. Manufacturers can successfully mitigate challenges if a component becomes unavailable by being aware of active alternates if they are included in their BOM.
3. Price Comparisons: Buyers often spend most of their time comparing part offers between suppliers and distributors. A simple but immensely beneficial aspect a BOM tool should possess is price benchmarking. BOM tools integrated with a digital marketplace can provide buyers with a wide range of offers from different sites and distributors through a search feature. Furthermore, a BOM tool should have filter options so buyers can quickly sort offers based on their requirements, such as price, availability, or manufacturer.
4. Order Tracking and Vendor Verification: The risk of counterfeit electronic components has increased, with scammers growing more sophisticated each year. To prevent suspect counterfeit components from entering your BOM and production line, a BOM tool should ensure component traceability through documentation such as order tracking, supplier data, shipment information, the quality management process a shipped order undergoes, and warranties for each purchase.
A BOM tool should list the supplier’s information up-front on all part offers. Likewise, it should identify which offers come from third-party suppliers, franchised partners, or authorized lines. With this information, buyers can assuage the risks of purchasing components from each.
Confirming that any component goes through a rigorous quality management system (QMS) before reaching your production line is critical. This lowers the risk of counterfeit components entering your supply chain and causing further delays or malfunctioning equipment.
5. Real-Time Shareable Data: Another overlooked vital attribute a BOM tool must possess is the ability to share real-time data quickly and understandably. With spreadsheet BOMs, it can be difficult to present them to team members without sufficient explanation. A BOM tool can help organize data that is legible and can quickly be shared with other members in your organization. This will increase team collaboration without sacrificing time to digest poorly displayed information on thousands of components that might be riddled with inaccuracies.
Now that we’ve discussed the attributes a BOM tool should have, is there one that can accomplish these tasks and more while being as cost-effective as Microsoft Excel or Google Sheets? Yes, there is.
Quotengine Capabilities
Quotengine is the premier BOM management tool for any original equipment manufacturers (OEMs), contract manufacturers (CMs), original design manufacturers (ODMs), electronic manufacturing service (EMS) providers, and more. Quotengine allows users to quickly upload their BOMs, with up to 4,000 line items, for a streamlined procurement process. Integrated with the leading digital marketplace for electronic components, Sourcengine, Quotengine can quickly pull offers from over one billion parts and provide active alternates.
Lengthy BOMs quickly receive all offers for corresponding parts with the ability to filter and find the best offer that matches your specific requirements. If a part doesn’t have an offer presented, that doesn’t mean it's completely unavailable. You can send Quotengine’s global team of experts an RFQ and they’ll source that pesky part for you.
Technical datasheets on part offers from over 3,500 suppliers are available for users. Additional data, including lead times, compliance data, FFF alternates, and component technical information, is readily available for users to review and share with team members for further discussion before committing to a purchase.
Manual processes and spreadsheets cannot handle the extensive, multilevel BOMs today. The more teams rely on these outdated processes, the more prone a company becomes to delays, recalls, and waste. A proper BOM management tool can quickly push a manufacturer ahead of the competition, and, better yet, it doesn’t even take days to learn. Quotengine ensures you can manage your BOM with time to focus on essential tasks outside of part orders. Ready to get started? Try Quotengine out now!
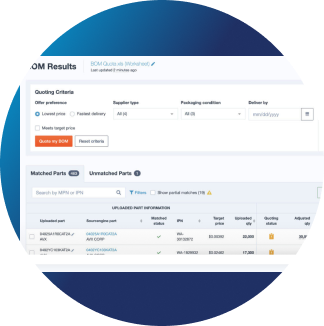
Quotengine: Your Ultimate BOM Tool
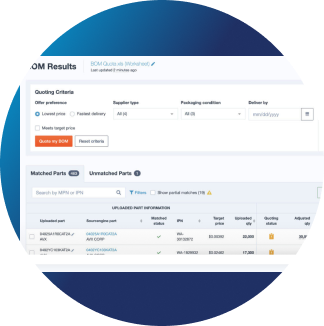
What’s Your Excess Worth?
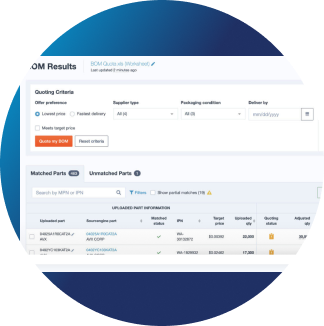
The Last Integration You’ll Ever Need
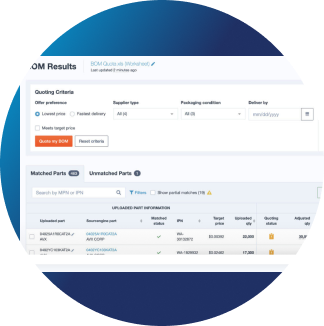
Sourcengine’s Lead Time Report
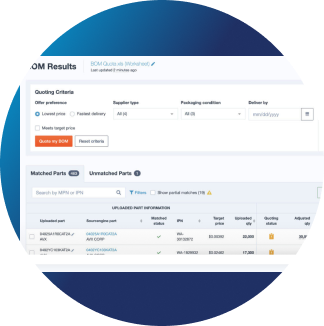
Sourcengine’s Lead Time Report
Your Lead Time Overview
Subscribe HereStruggling with excess inventory?
Download your free copy!.png)