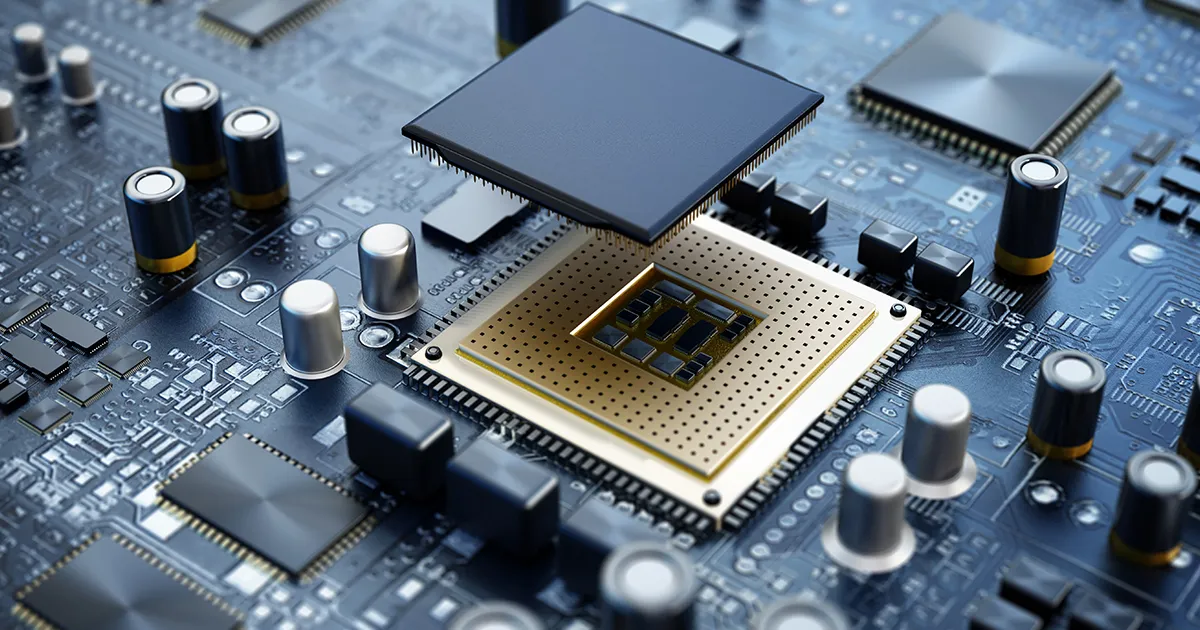
If you’re a part of the electronic component supply chain, whether a design engineer, buyer, or manufacturer you know there is one inherent truth about the industry. The supply chain is a fragile beast, fraught with instability that is often prone to sudden and dramatic shifts. Market changes, geopolitics, global depressions, inflation, wars, and even a ship getting stuck in the Suez Canal can have massive rippling effects on electronic component supply.
Component availability, at least before the 2020-2022 global semiconductor shortage, was determined by a specific set of requirements. Prior year demand and a limited market forecast would aid original component manufacturers (OCMs) in determining production capacity for electronic component lines the following year. Before the pandemic, component sourcing and production capacity determination hardly required devoted strategies.
Shortages and end-of-life (EOL) components were risks but historically did not last as long or hit as hard as the global semiconductor shortage. Now, the supply chain is experiencing sharp and sudden shifts, from electronic component scarcity to surplus. Component availability has become more complex as new factors such as long-lasting component shortages, faster component obsolescence, and regulatory compliance requirements impact it.
Strategically pre-planning for these occurrences as early as the product design phase is necessary for original equipment manufacturers (OEMs), electronic manufacturing service providers (EMS), and others. But what does that entail?
Making a product more resilient against supply chain risks and component availability challenges means removing sole source components–electronic components with no alternates–and finding equivalent electronic components for others. Pre-planning equivalent electronic component crosses can help speed up engineering approval, better manage the product lifecycle, control costs, and prevent production stalls.
Equivalent Electronic Components vs. FFF Alternates vs. DIR Components
Equivalent electronic components, form-fit-function (FFF) alternates, and drop-in replacements (DIR) are all critical in production. Numerous instances outside of component obsolescence and shortages require an alternate component. The number of electronic components used within products is increasing. Vehicles, for example, can use upwards of 3,000 components per car. That’s a lot of components that might not always be in stock, especially if the needed components are always in high demand by a myriad of industries.
With the rate of innovation within the electronic component industry, it is not uncommon for a newly designed component to suddenly not be recommended for new design (NRND). Likewise, experts believe many components will soon be entering EOL due to the 2020-2022 shortage and the 2023 chip glut. That is a lot of stock to find alternates for quickly.
That said, not all electronic components are created equal. The more common a component is, such as passives or discrete transistors, the more likely it is to find a DIR component, one of the best options when replacing an unavailable electronic component. But why is a drop-in replacement better than an FFF alternate? Sometimes a component simply has a list of FFF alternates and not equivalent components.
The differences between the three main types of alternate components can be almost indiscernible to abundantly clear:
- Equivalent Components: These electronic components have the same or nearly the exact electrical specifications as the missing component. Equivalent electronic components may have noticeable differences, such as extra features or different packaging. Engineering teams have to ensure the component's functionality by evaluating and approving its design. Minor redesigns might be required.
- FFF Alternate Components: These electronic components may not possess the same electrical specifications, pinout, packaging, symbol, or features as the desired component. However, FFF alternates can be configured to function the same way as the electronic component that needs replacement. Engineers usually must evaluate and make design changes to utilize the FFF alternate within the product.
- DIR Component: These electronic components have the same symbols, pinout, PCB footprint, and parametric features as unavailable electronic components. They may lack a similar MPN, but their similarities can serve as direct, interchangeable equivalent electronic components in the product design without any necessary redesigns or design engineer evaluation.
During component unavailability, the best option is to find a DIR component. Drop-in replacements effectively bring any additional cost and time for redesigns to zero, if any at all. Unfortunately, not all electronic components are common enough to have DIR components on standby. Finding suitable direct equivalents or FFF alternates is the next best option. Either of which, even FFF alternates with many distinct dissimilarities to your unavailable components, can serve the same functionality.
It is often better to redesign around an available alternative than have no components at all.
The more specialized or uncommon a component is, the less likely DIR alternates are readily available. Specific components like DDR SDRAM modules, such as Micron Technology’s MT46V16M16CY-5B, have exceedingly specialized footprints. Replacing a DDR SDRAM module like Micron’s would require a broad redesign for any FFF alternate. Most specialized ICs can take hours to find a better alternative.
How to Find Alternate Electronic Components
Searching and finding alternate electronic components can take a long time. Manufacturers will need teams to sift through thousands of data sheets to compare hundreds of different components that can range in scarcity to find the perfect cross-reference match. It can be time-consuming if a product requires hundreds, if not thousands, of components to complete.
The best way to begin your strategy for finding equivalent electronic components is to locate drop-in replacements first. If there are none or they are currently unavailable, look for variants by utilizing a component’s MPN. If no results come up, search by electrical ratings and component type.
Once you find your equivalent, FFF alternate, or drop-in replacement, the selection process should involve evaluating component data sheets and comparing part specifications and critical attributes. If the alternate passes an engineering evaluation, one must ensure it is a feasible replacement. This means confirming there are verified suppliers with available stock.
Last but not least, studying the historical trends of a component, their price and lead time, alongside their lifecycle status, to determine whether an equivalent electronic component is recommendable due to vulnerability to volatile changes. Each step is a time-consuming and tedious task to complete but necessary when ensuring product design resiliency.
It’s why one of the best things you can do to increase time efficiency without sacrificing resilience is to locate alternatives and replacements during the initial product design. Likewise, one should use digital tools to monitor market shifts, keep track of component availability, and alert engineers to possible design risks during component selection.
Sourcengine API and market intelligence tool, Datalynq can accomplish these monumental feats. All of this can be accessed without leaving your ERP system.
Once you find your alternates, you can purchase them immediately from within your ERP with access to over 1 billion offers on Sourcengine’s e-commerce platform. When combined with market intelligence from Datalynq, you can strategize long before time is of the essence.
Datalynq analyzes real-time market data from Sourcengine to aid engineers and other supply chain decision-makers in making the best-informed decision during product design. Datalynq can score product design risk based on the components in your BOM through its part management feature, helping users identify components that pose the most significant overall risk alongside FFF and DIR alternates for components in case of future unavailability.
Using both digital tools help create a more robust supply chain and fortifies your product design against future shortages. According to the experts, these shortages are only going to get worse.
Sign-up for Datalynq or talk to our experts to learn how to benefit from Sourcengine API and Datalynq today.
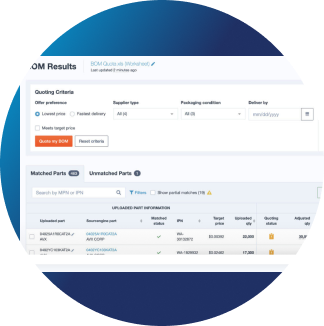
Quotengine: Your Ultimate BOM Tool
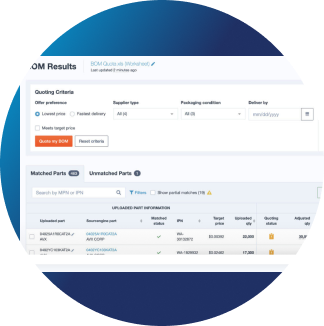
What’s Your Excess Worth?
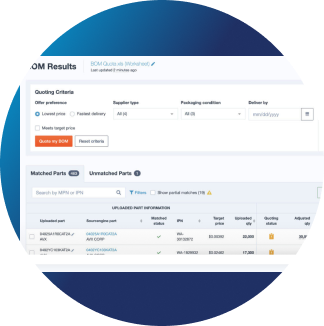
The Last Integration You’ll Ever Need
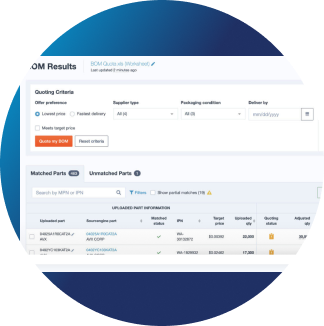
Sourcengine’s Lead Time Report
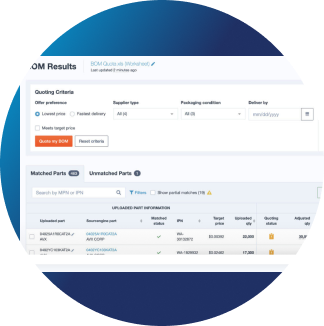
Sourcengine’s Lead Time Report
Your Lead Time Overview
Subscribe HereStruggling with excess inventory?
Download your free copy!.png)