
On April 3rd, Hualien residents were preparing for another warm, sunny day when the strongest earthquake since the 1999 Jiji earthquake occurred. At 7:58 am, a 7.4 earthquake struck 15 miles off the coast of Hualien City, leading to landslides, power outages, and a tsunami warning. Over 1,100 people were injured with 16 tragically losing their lives.
There is a silver lining in the devastation. The earthquake’s epicenter was located on the eastern coast of Taiwan, away from more populated cities such as New Taipei and Taichung. This limited the destructive possibilities of what could have been. Situated on the Pacific Ocean’s Ring of Fire and its proximity to the convergence of two tectonic plates, Taiwan has become quite familiar with the effects of earthquakes.
It’s one of the reasons the United States and others have grown concerned over Taiwan’s abundance of semiconductor facilities. Taiwan, home to chip powerhouse Taiwan Semiconductor Manufacturing Corporation Limited (TSMC), is the largest producer of semiconductors globally. TSMC makes over 60% of the world’s semiconductors and over 90% of the most advanced chips. While TSMC has been expanding its locations worldwide since the global semiconductor shortage, it is still the undisputed leader in raw semiconductor manufacturing.
This is also a problem.
Typically, when one thinks of the problems that arise when there is a lack of geopolitical diversity, one focuses on the political side of “geopolitical.” An example of these problems could be increased volatility between two countries, leading to sanctions or other trade restrictions. This is seen in the ongoing trade war between the United States and China.
The “geo” portion and its inherent challenges are often overlooked. In the past, natural disasters and severe weather events were much rarer. These natural disasters may be labeled as “billion-dollar” weather events due to the financial cost of the damage they incur. Over the last several decades, the occurrence and severity of natural disasters have increased. This can be attributed to climate change and expanding population. If more people are around to be affected by natural disasters, the cost of its destruction will increase.
Earthquakes Shake Up Industry in 2024
The semiconductor industry has been shaken up by two major earthquakes in 2024 alone. New Year’s Day began with a 7.5 quake in Noto, Japan. Like Taiwan, the earthquake was the strongest quake to hit mainland Japan since the 9.0 undersea megathrust quake in 2011. The 2011 Tōhoku earthquake and subsequent tsunami led to the widely known Fukushima Nuclear Accident after flood waters damaged the power plant. Both earthquakes led to millions in damage and thousands of casualties.
Japan and Taiwan are no strangers to earthquakes given their locations. Both countries have heavily invested in earthquake preparedness, but highly destructive forces of nature can still impact the best laid plans. Furthermore, Taiwan and Japan are uniquely situated within the global semiconductor supply chain, not only as leaders, but surrounded by the high concentration of semiconductor manufacturing within Asia-Pacific.
After the Noto Earthquake, Global Wafers, Toshiba, Murata Manufacturing Co., Ltd., Tower Semiconductor, TSMC, United Microelectronics, and Power Technologies shut down production to assess for damage. Depending on location, chipmakers were able to resume production immediately or fix very limited damage
While the harm to Japan’s semiconductor facilities was minimal, even small factory shutdowns can have wide-reaching effects on the global supply chain. Unlike other industries, it takes time for chipmakers to ramp up production after a complete shutdown. Semiconductor fabrication is a lengthy and complicated process, sometimes requiring over 500 steps to produce one component. The littlest tremor can ruin hours or days of work, as raw wafer manufacturing is particularly sensitive to seismic activity.
Since the Noto Earthquake occurred during the semiconductor industry’s typical low season, its effects on the more significant supply chain were limited. The impact was controllable, and long-lasting effects were thankfully avoided.
These results are not always the outcome of natural disasters.
While Taiwan’s quake was on the less populated side of the island, damages have impacted some of the many chipmaking facilities there. Micron Technology has recently stated that the quake will impact its DRAM supply for a calendar quarter by 4%-6%. It has not returned to total production capacity for DRAM following the earthquake, with supply-demand already tight from strategic production cuts throughout 2023 and early 2024. There is no word on if the quake will impact Micron’s coveted high-bandwidth memory (HBM) supplies.
Thanks to earthquake location and building resistance damage has been minimal, but the tremors have reignited concerns over manufacturing location diversity. For years, the United States has stated that Taiwan should expand operations outside the island due to its propensity for earthquakes. Taiwan’s chipmaking companies have hesitated to do so because of the country’s “silicon shield,” which acts as a buffer to discourage its larger neighbor from making any outwardly aggressive moves.
Unfortunately, the more concentrated semiconductor facilities are in one place, the more vulnerable they are to disruptions. This is especially true for black-swan events like natural disasters that often occur with little warning at inopportune times.
During the shortage, pandemic lockdowns in Xi’an and severe winter weather in Texas contributed to shuttered facilities. Unlike the Japan and Taiwan earthquakes, these biological and natural disasters occur during heightened demand for components on a stressed global supply chain. Operations were halted for days, adding weeks to already extended lead times. Even a drought in Taiwan during the global semiconductor shortage caused facilities to limit production, adding strain to the worldwide supply, as water limits dictated production output.
If one of these dense semiconductor manufacturing locations were to experience severe destruction and become inoperable for months, it would profoundly impact the entire global supply chain. A statement by the Semiconductor Industry Association (SIA) at the height of the pandemic still rings exceedingly accurate today.
“If Taiwan could not make chips for a year, it would cost the global electronics industry almost half a trillion dollars in revenue. The global electronics supply chain would come to a halt."
Geographical Diversity is Required
Aside from the location of Taiwan’s 7.4 earthquake, the country’s preparedness also helped avoid a worse outcome after the 1999 earthquake. The 1999 earthquake disrupted the electronic components industry for weeks when chips were not essential to the global economy. If such an event occurred now, it would be catastrophic industries and economies alike. After the 1999 Jiji quake, Taiwan and its companies stepped things up.
TSMC says that its buildings are designed well beyond code for earthquake resilience. This is imperative for TSMC considering how critical the chipmaker is to the global supply chain. Its twelve fabs in Taiwan could cripple the global economy should they all go offline.
However, it’s important to note that Taiwan is not alone in its proximity or susceptibility to natural disasters. South Korea, another giant in memory semiconductor manufacturing, is at risk for major storms and flooding. As climate change continues to impact the globe, South Korea is becoming more vulnerable to severe weather. Even the United States, pushing to grow its own semiconductor ecosystem, is no stranger to earthquakes, droughts, hurricanes, and tornadoes.
2023 was a record-setting year in the United States for billion-dollar weather and climate disasters, with a total of 28, easily surpassing the previous record of 22 in 2020. Since the 1980s, the United States has seen massive growth in natural disasters, with 137 separate billion-dollar disasters occurring between 2017 and 2023. This does not even cover the global rise in harsh weather over the last few decades.
So, how does the semiconductor industry increase resiliency against the unpredictable? Geopolitical diversity.
Each country, down to its cities, can be affected by different weather disasters depending on its location. Taiwan is more at risk of earthquakes than supercells compared to Tornado Alley, USA. Despite working toward more sustainable practices to limit our effect on the world’s climate, natural disasters cannot be eliminated. To create a more resilient global supply chain, companies and governments must work together to make the semiconductor industry more “global.”
Thankfully, the industry is moving toward a more united worldwide ecosystem. The semiconductor shortage revealed the problematic nature of geopolitical dominance. As a result, numerous governments have approved of subsidy programs over the last year to help chipmakers. Taking the brunt of the financial burden off original component manufacturers (OCMs) has encouraged many organizations to take the plunge and invest in new facilities.
With a greater expanse of the global supply chain and strong, domestic ecosystems to support it, should one area be ravaged by natural disasters, it will not derail the global supply chain entirely.
Access a Global Distributor Network with Sourceability’s Sourcengine
New facility plans take time, and during their construction, it is pertinent that companies work alongside distributors who have access to various electronic component markets. A negative aspect of a more global supply chain is trade restrictions that might impact one region over another. While greater diversity will eventually give procurement teams more options, OCMs currently favor new facilities in countries that are already semiconductor leaders such as Taiwan, South Korea, China, the U.S., and Japan. Two of which are in a heated trade war.
There is a solution. As a global electronic components distributor, Sourceability can ship anywhere. If you need a component that only ships to Europe, but you are based in North America, Sourceability can help your company get it. This can make some electronic components cheaper if tariffs impact price.
Sourcengine, Sourceability’s leading e-commerce site, hosts over 1.6 billion electronic component orders from more than 3,500 franchised, authorized, and qualified third-party suppliers. With our worldwide team of experts, our staff can help organizations find even the hardest-to-source components. Upload your bill of materials (BOM) to Sourcengine’s BOM management tool, Quotengine, to find offers for parts listed on your BOM.
If none of your requirements are met, you can contact our team for a personalized RFQ for the parts needed. Ready to get started with Sourcengine?
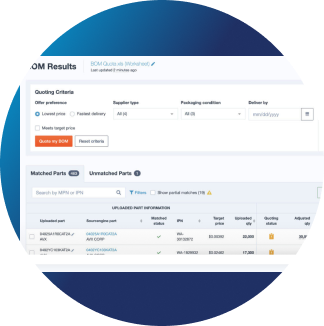
Quotengine: Your Ultimate BOM Tool
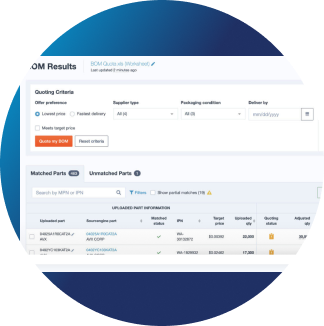
What’s Your Excess Worth?
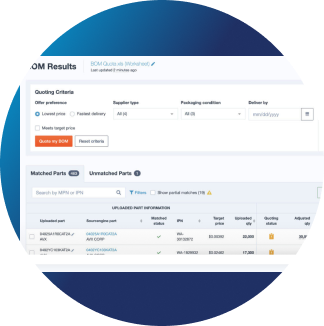
The Last Integration You’ll Ever Need
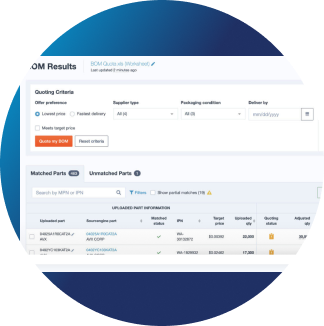
Sourcengine’s Lead Time Report
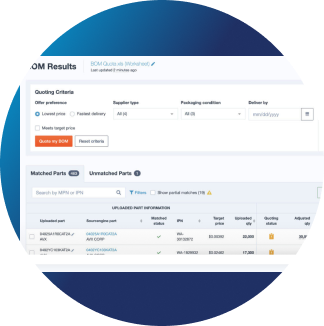
Sourcengine’s Lead Time Report
Your Lead Time Overview
Subscribe HereStruggling with excess inventory?
Download your free copy!.png)